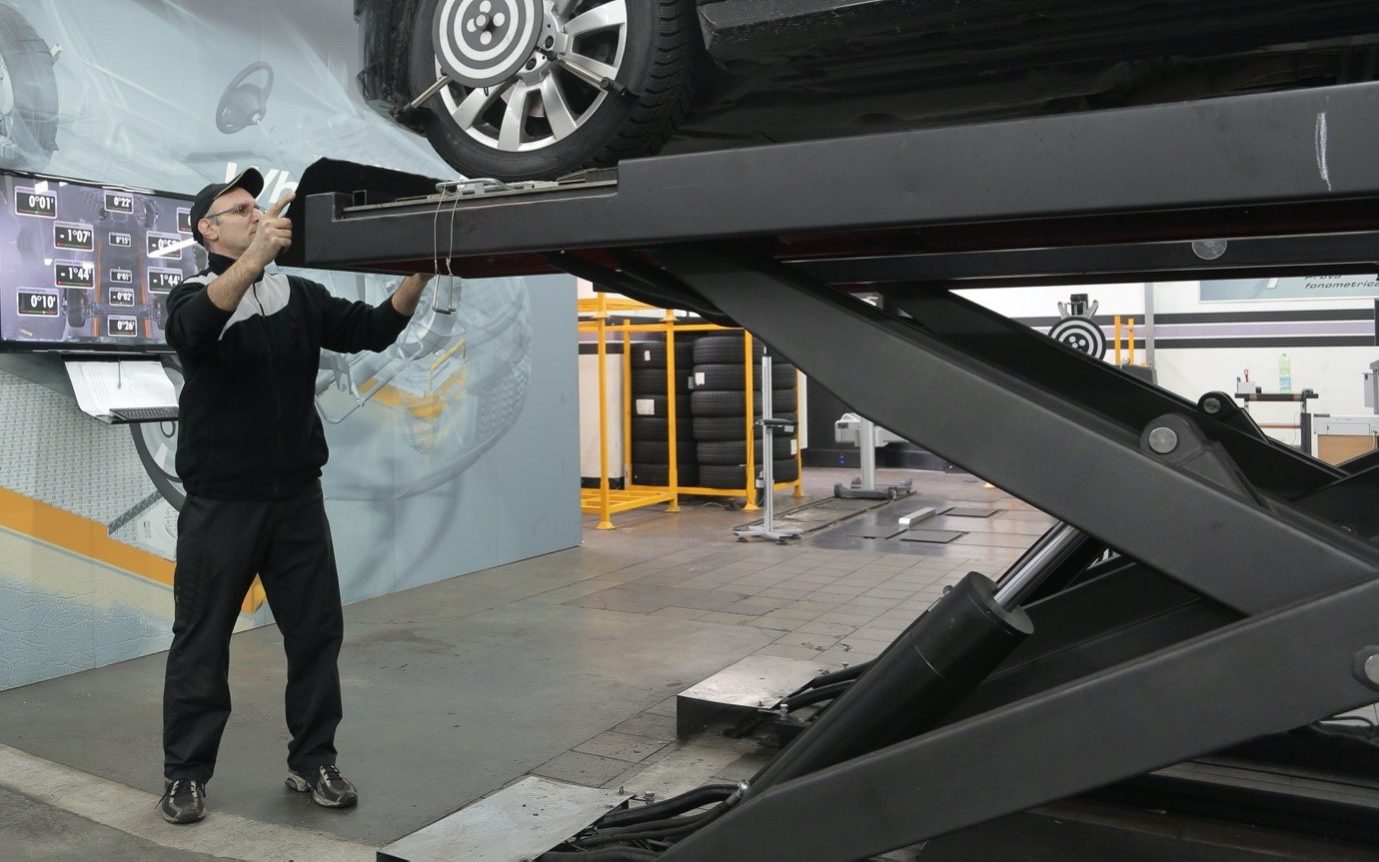
As humans, we all make mistakes, and no one is perfect. Human error has been the root cause of many quality problems in industries such as aviation, nuclear, marine, construction etc.
In common knowledge, an error caused by the human factor occurs when there is a general agreement that a person should have done something other than what he or she did. People are prone to mistakes (unintentional or intentional) as a result of one or more of a range of human factors – fatigue, distraction, pressure for example.
Human factors are things, which affect people, their performance, and their interaction with processes, equipment and the working environment. In simple words, Human Factors is ‘fitting the man to the job, and the job to the man’. The aim of the human factors concept is focused on reducing and capturing human errors. Unintentional human errors involve:
- MISTAKES – the person didn’t know what needed to know (knowledge-based, failure of expertise),
- LAPSES – something that a person has forgotten to deal with (memory-based), and
- SLIPS – the person had the correct solution, but executed it incorrectly (attention failures, misapplied competence).
Avoidable errors caused by human factors have led to devastating consequences. Here are some reasons why human factors are important in all industries.
1. Safety
One of the most critical consequences of human errors is safety issues. The human factors concept is given huge importance on quality management systems for the Aerospace industry (AS 9100), compared to the general ISO 9001. Avoidable errors have caused major safety incidents in aviation. In 1988, Aloha Airlines had a massive safety issue, as the cabin structure ripped away during the flight. It occurred because the inspectors were complacent and did not spot the cracks in the structure.
To increase safety within the aviation industry, the Mandatory Occurrence Reporting system has been implemented. The purpose of the system is to enhance passenger safety. MORs ensure that the relevant safety information pertinent to civil aviation is properly reported, stored, collected, protected, disseminated, exchanged, and analysed, and the goal is not to attribute liability or blame.
2. Quality
Moving on from safety, human factors are also important in determining the quality of products and services supplied to consumers. Companies are beginning to realise the impact of having a robust quality management system to help prevent human errors that impact the quality of their products.
Businesses are increasingly engaging the services of expert quality management consultants to help them develop a robust QMS system. These experts are well-versed in both – general ISO 9001 standard and aerospace AS 9100 and help businesses to comply with relevant requirements. The end goal of having a QMS is to ensure customer satisfaction. Often, human errors lead to quality issues, which results in a bad customer experience. As a result, a business might lose important sales as customers will flock to competitors for better quality.
You don’t need to be in the aviation industry to realize that human factors can impact quality. A restaurant can have dire consequences if its head chef commits avoidable errors that impact the food quality. Furthermore, poor customer service may lead to business failures and shutdowns in service-related industries.
3. Consistency
Quality and consistency are linked. Human errors can lead to inconsistencies within a product range. Therefore, businesses pay a lot to employ a quality control mechanism. This ensures that all products coming from the production line are of the same quality.
Even though the human factor concept is strongly present in the aviation industry, major businesses in other industries are also beginning to understand the importance of mitigating avoidable human errors. Hence, they’re employing robust quality management systems to help them achieve their business goals.
4. Employees mental health
One of the most important trends in business in 2021 according to Business Insider will be taking care of mental health. Not only pandemic will be a global problem, but also loneliness and depression. Pandemic is a significant source of anxiety, stress and uncertainty. According to EASA and ICAO stressors within the aerospace industry include:
- stress at a personal level, social unrest and prolonged uncertainty of not knowing when life may return to a more relaxed state,
- economic pressures of returning to service and economic survival at an organisational level,
- loss of experienced personnel due to furlough and redundancies, remaining personnel may feel unsafe returning to duty with a higher than normal psychological stress and worries about unemployment,
- task distraction or interruption during working from home periods, not following instructions or requirements,
- working additional hours causing overload or fatigue, due to reduction in the number of personnel,
- isolation of operational staff from administrative and commercial management staff,
- reduced people’s ability to work collaboratively due to working from home (problems with team-working and communication),
- skills and knowledge degradation due to lack of recent practice,
- backlog in training with an effect on performance.
All of this may impact the personal wellbeing of professionals and be a considerable source of anxiety for employees causing an increased probability of human errors.
Organisations need to understand those risks and develop strategies to mitigate them. This can be done by implementing a robust QMS, which sometimes can become complicated. Therefore, it is good to consult experts such as EQM consult, who can help you devise a strong quality management strategy. We provide internal quality audits, to help you identify loopholes and human errors in your operations. Furthermore, we also help to implement quality management systems that comply with ISO 9001 and AS 9100. You can check our website for more information about the services, or contact us for a consultation.
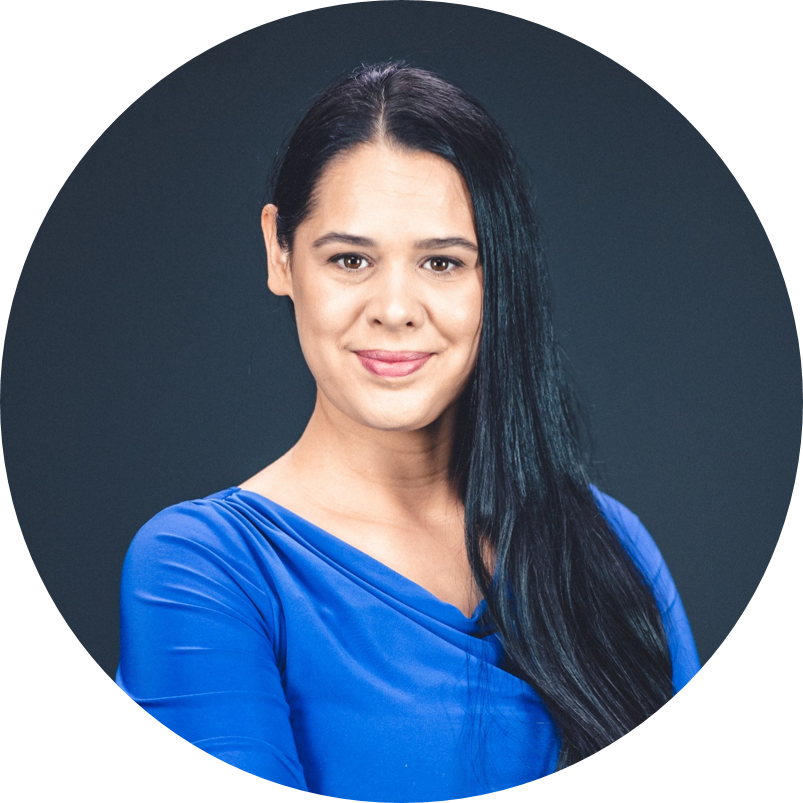
Ph.D. Beata Paliwoda
Founder and Owner of EQM. Environmental and quality consultant and auditor. Professional career built in Quality Assurance departments in various companies from the automotive, aerospace, railway industries, as well as a management systems consultant. Successfully completed many complex projects related to the implementation of management systems, process improvements and business transformation. Auditor of ISO 9001, ISO 14001, AS 9100, project manager of APM, lecturer at the Poznan University of Business and Economics, researcher on the effectiveness of EMS and QMS in organisations.