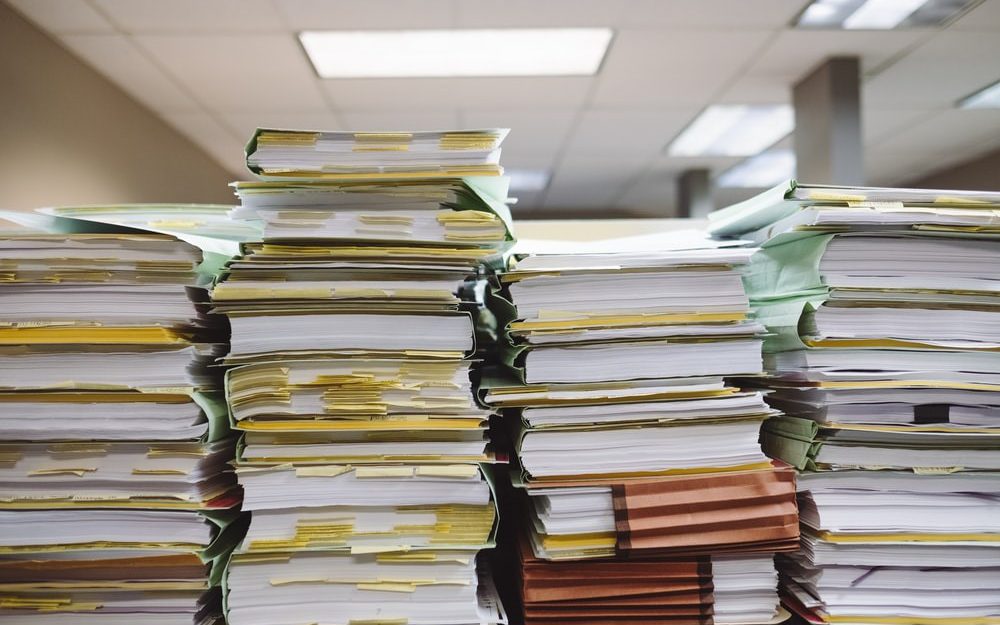
When creating a quality management system, you’ll come across various types of document types.
Within a standard QMS, you’ll typically find documents such: Policies, Processes, Procedures and Work Instructions. It is easy to get overwhelmed with the sheer amount of documentation you need to maintain in a QMS. You may even be questioning yourself at every stage about why there’s a need to create such documentation and follow it rigorously.
Here are some reasons why following your approved documentation is crucial for successfully implementing a quality management system.
1. Ensures The Implementation of Quality Standards
Obtaining the ISO 9001 is the first step; however, it is crucial to maintain the documented QMS throughout your organisation. Your employees can refer to the relevant documents if they need to understand the relevant QMS process or procedure. Once understood, they’ll implement such practices in their work, translating into higher product quality.
2. Reduces The Potential for Error
Errors are bound to happen, and there is an increased risk if your quality management system is not properly documented. Your staff wouldn’t have access to the policies or procedures to help them during operations. As a result, there would be an increased chance of errors that would impact product or service quality.
Therefore, having a documented QMS is beneficial as it will help minimise the risk of errors. Employees will readily have access to such documents, and it would help them work according to the company’s QMS.
3. Monitoring & Analysis
Constant monitoring, analysis and consistent improvisation are the hallmarks of a good quality management system. However, it can be hard to monitor product quality and efficiency if you don’t have a documented QMS system. Such documents allow you to monitor business processes and ensure they’re complying with the relevant standards and requirments.
Once monitored, you can analyse your process and can come with plans to improve inefficient workflows. It will also help you to stay compliant with the relevant ISO requirements.
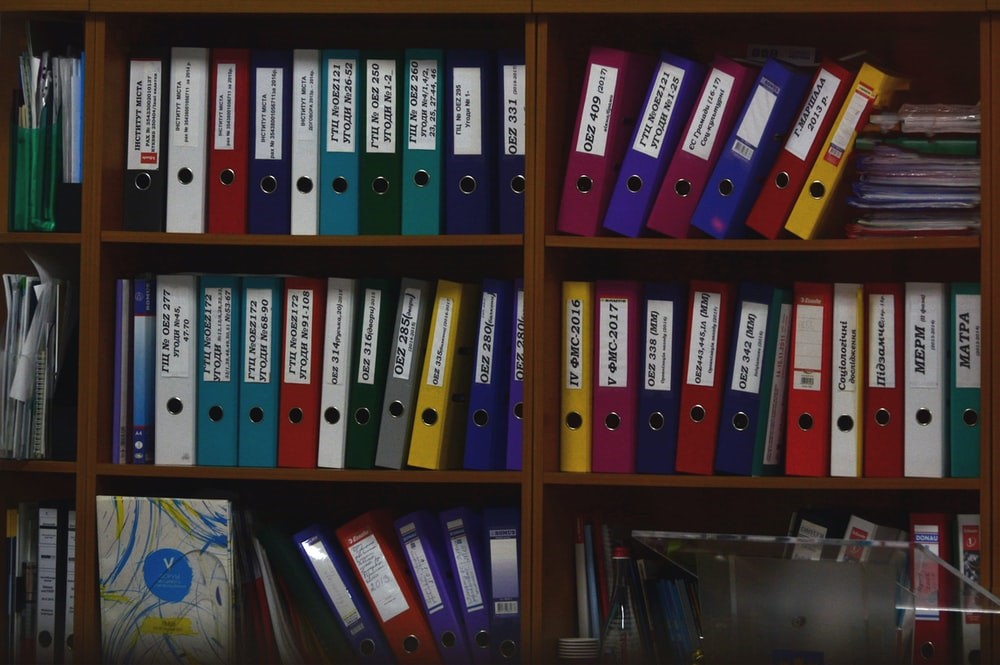
Filename: physical-files-cabinet
Alt-text: a stack of physical files in a cabinet.
4. Fulfilling Regulatory Purposes
As mentioned, document creation and control are an essential part of any QMS and is a requirement of ISO 9001. The standard makes it compulsory for businesses to maintain a documented information and have it available for use within an organisation. It also emphasises having the right people to access it wherever and whenever they need it. Any unauthorised access or changes in the documentation by irrelevant personal is frowned upon.
The documentation, maintenance and control of processes, procedures and SOP’s is up to the business. There is no set way of documenting QMS; it just needs to adhere to the relevant standard.
Creating and maintaining a robust QMS can be hard, and you may need expert outside help to ensure compliance. If you’re looking for an external quality management specialist, then contact us at EQM Consult. As a boutique management consulting firm specialising in environmental management systems and quality management systems, we can help your business comply with ISO 9001, AS 9100 and ISO 14001 standards. You can check our website for more information about the services, or contact us for a consultation.

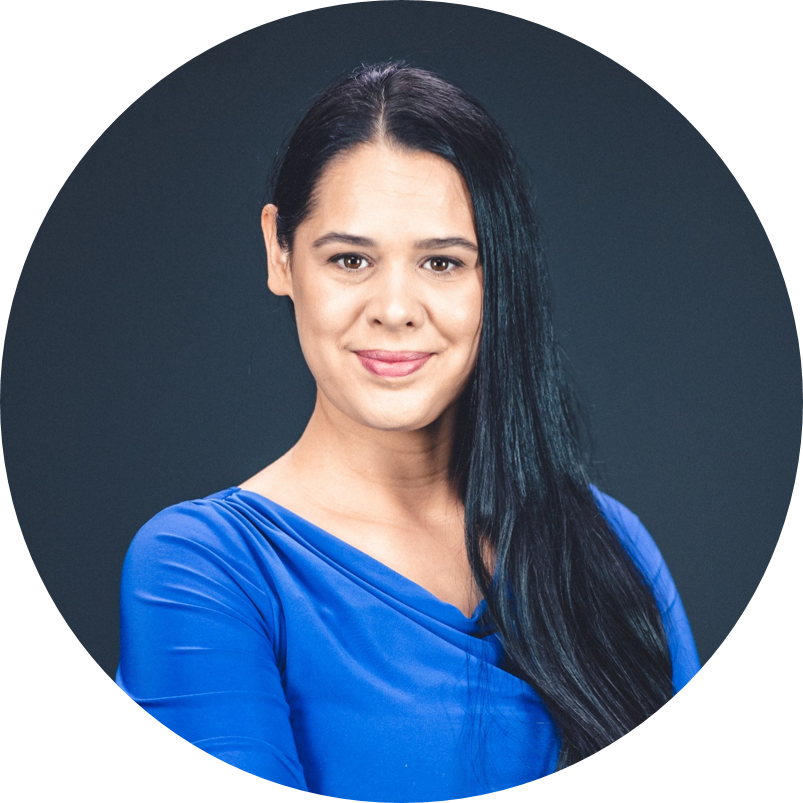
Ph.D. Beata Paliwoda
Founder and Owner of EQM. Environmental and quality consultant and auditor. Professional career built in Quality Assurance departments in various companies from the automotive, aerospace, railway industries, as well as a management systems consultant. Successfully completed many complex projects related to the implementation of management systems, process improvements and business transformation. Auditor of ISO 9001, ISO 14001, AS 9100, project manager of APM, lecturer at the Poznan University of Business and Economics, researcher on the effectiveness of EMS and QMS in organisations.