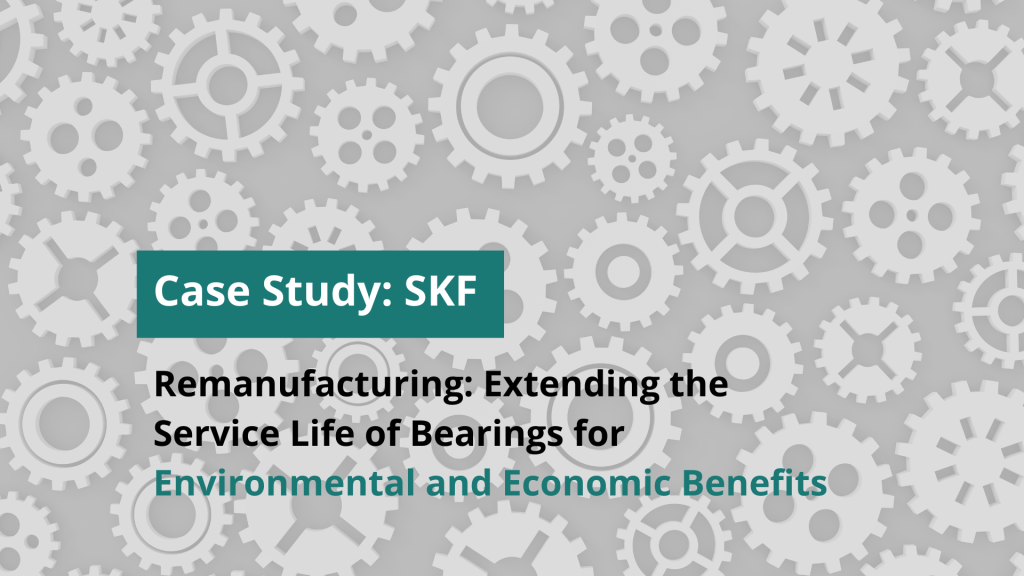
The service life of bearings often falls short of the calculated lifetime due to various application conditions, including contamination and metal-to-metal contact. Wear, rust, indentations, and microcracks are common damages that significantly reduce their lifespan. However, there is a solution to prevent premature bearing failure and improve environmental sustainability while reducing costs. Remanufacturing, a process that refurbishes bearings before major damage occurs, offers a promising approach. This article explores the benefits of remanufacturing, its impact on environmental aspects, and the economic rationale behind its adoption.
Case Study: SKF
Best Environmental Management Practice
Remanufacturing plays a vital role in extending the service life of bearings. By refurbishing worn-out bearings, remanufacturing significantly reduces costs and lead times. Additionally, this practice presents a notable environmental advantage by requiring substantially lower energy and raw material use compared to the construction of new bearings.
SKF, a leading bearing manufacturer, employs robust remanufacturing processes to repair relevant functional surfaces and replace components when necessary. The company’s adherence to bearing manufacturing standards, processes, equipment, and quality assurance ensures superior results, even for extensive remanufacturing requirements. Advanced traceability is achieved through a management system that uniquely marks each asset throughout the remanufacturing process.
SKF goes beyond standard remanufacturing by offering the option to bring bearings to new or higher specifications. This includes mounting sensors, integrating lubrication and sealing solutions, and reworking bearings to meet specific requirements. Furthermore, advanced monitoring systems are implemented to detect failures immediately after their appearance, improving the overall remanufacturing process.
Environmental Aspects Affected
Remanufacturing drastically decreases the energy consumption associated with bearing production. Depending on the extent of remanufacturing required, up to 90% less energy is utilised compared to manufacturing a new bearing. Moreover, responsible cleaning of used bearings and appropriate waste management contribute to reduced environmental impact.
Rationale / Economics
Besides the environmental benefits, adopting remanufacturing practices yields significant economic savings. Cost-benefit analyses demonstrate that bearing size, complexity, condition, and price play a crucial role in achieving substantial cost reductions. By opting for remanufacturing, businesses can effectively manage their expenses while ensuring high-quality results.
In conclusion, remanufacturing offers a sustainable solution to extend the service life of bearings, reduce costs, and minimize environmental impact. With SKF’s expertise and commitment to quality, businesses can reap the economic benefits while contributing to a greener future. By embracing remanufacturing practices, industries can demonstrate their dedication to environmental responsibility and resource efficiency.
Download Free Guide on Best Environemntal Management practices in Fabricated Metal Product Manufacturing Industry that will help you to save on costs and be more eco-friendly.
If you would like to achieve benefits and integrate your business processes with the best environmental practices through the implementation of the Environemntal Management System according to ISO 14001 – visit www.iso14001in14weeks.co.uk – I will be happy to help!
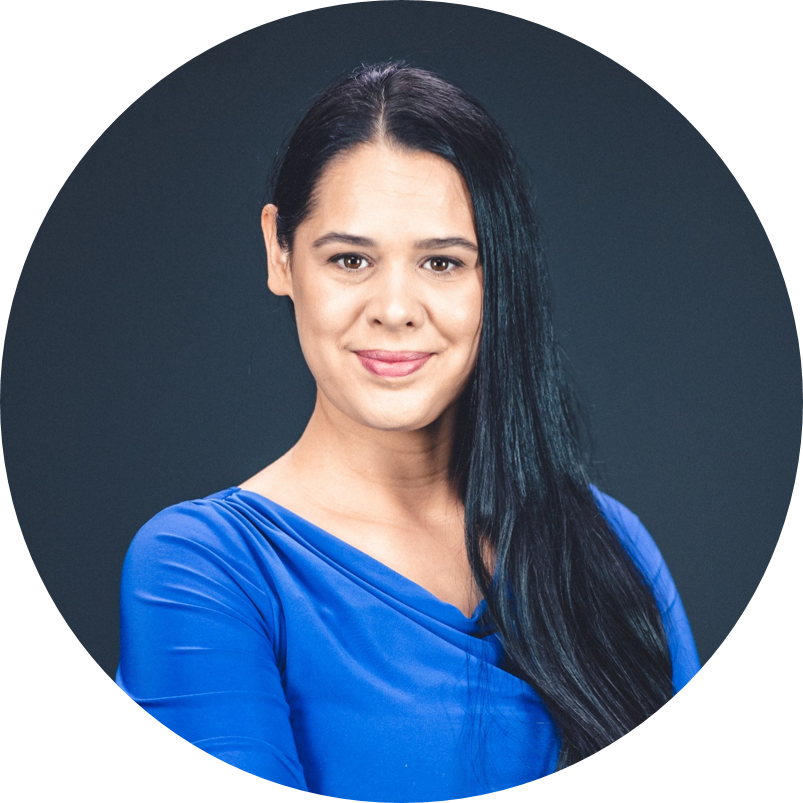
Ph.D. Beata Paliwoda
Founder and Owner of EQM. Environmental and quality consultant and auditor. Professional career built in Quality Assurance departments in various companies from the automotive, aerospace, railway industries, as well as a management systems consultant. Successfully completed many complex projects related to the implementation of management systems, process improvements and business transformation. Auditor of ISO 9001, ISO 14001, AS 9100, project manager of APM, lecturer at the Poznan University of Business and Economics, researcher on the effectiveness of EMS and QMS in organisations.
Sources
- European Commission, Best Environemntal Management Practices for Fabricated Metal Product Manufacturing, EUR 30025 EN, 2020, doi:10.2760/894966
- https://www.skf.com/uk
Disclaimer
The purpose of this blog post is to promote best environmental management practices and showcase a real-life example of sustainable initiatives. The information provided is based on available sources and is intended for general informational purposes only. The author does not assume any liability for the actions or decisions made by other organisations or individuals based on the content of this blog post. The author also does not claim to have been directly involved in the implementation of the described practices within the specific company mentioned.