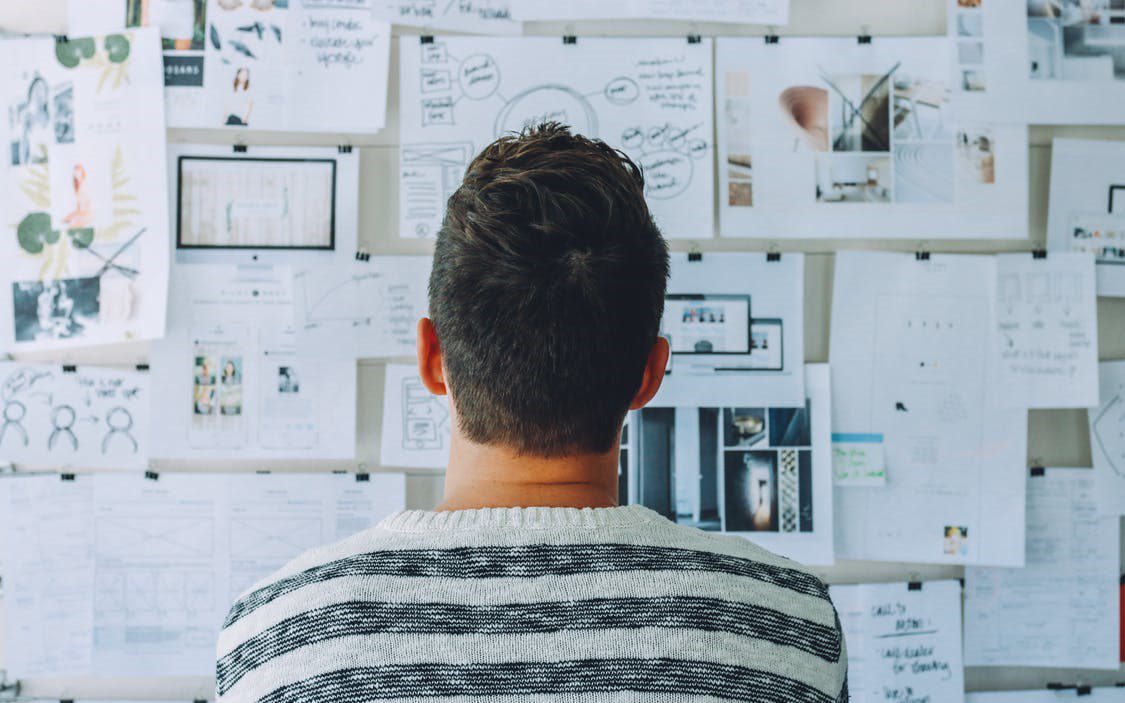
Advanced Product Quality Planning (APQP) in the aerospace and automotive industries plays a crucial role.
The aerospace APQP is based on AS 9145 standards. The APQP concept comes from the automotive industry and has been modified for the aerospace application to face challenges and uniqueness of the aerospace industry (low volume – high mix, long life cycles, high level of regulation).
What is APQP?
Simply put, APQP is a framework very similar to the Six Sigma model, consisting of a set of procedures designed around product development and industrialisation. Since the aerospace and automotive industries are extremely competitive and put high pressure on conformity, the core competing factor lies in the quality of the product as opposed to the time or costs that are associated to make it.
With complex supply chains and the introduction of new products posing a threat and opening a gateway of possibilities that can end in a loss or failure, an Advanced Product Quality Planning (APQP) ensures a system is in place to introduce products centered around customer satisfaction.
The APQP framework begins with the conceptual product needs and extends through product definition, production planning, product and process validation, product use up to post-delivery activities. The aerospace APQP has five standard phases based on PDCA circle.
- Phase 1. Planning
- Phase 2. Product Design and Development
- Phase 3. Process Design and Development
- Phase 4. Product and Process Validation
- Phase 5. On-going Production, Use and Post-delivery Service
The APQP standard AS 9145 integrates and collaborates with the requirements of other well-known and widely-used aerospace industry standard such AS 9100, AS 9102, AS 9103 or AS 9110.
Here are 4 reasons why Advanced Product Quality Planning in aerospace is important.
1. Delivers Quality Product On-Time at Lower Costs
The APQP approach ensures that the design of the product is influenced at early stages of development. This is possible because techniques such DFM (Design for Manufacture), DFM&O (Design for Maintenance and Overhaul) and PRR (Production Readiness Review) are integral part of the framework.
When a lot of time and effort has been put into the planning of the quality of the product well before the processes have even begun, it gives a lot of time for any back-and-forth before the final quality of the product is approved.
A uniform approach guarantees that quality products are delivered on time and satisfies costs and performance targets. This may be achieved by reducing process variation and anticipating risks and defects at early stages.
2. Offers Early Identification for Change
One of the reasons why you should really consider incorporating the Advanced Product Quality Planning is that it allows the early identification of any change that may be required.
Since the planning is done way ahead of time, it gives you time to come up with mitigation strategies or propose and incorporate changes where required. It also provides you with time to implement the risk mitigation strategies you may have had already planned.
Changes could be either intentional or incidental depending on whether they’re based on enhancing customer satisfaction or on factors such as customer usage, the environment, etc.
3. Customer Satisfaction Is the Priority
The entire purpose of Advanced Product Quality Planning is to ensure customer satisfaction while meeting the compliance obligations. Customers are the end receivers of your product and this is exactly why APQP is crucial for an industry like aerospace. The application of APQP shall contribute to the shorter lead-time by reducing waste and rework and better capacity management.
All resources are directed keeping in mind what the customer requires. Launching your product in the market after running it through APQP also limits the risk and changes that may be required later on because the product was already carefully tested and validated.
4. Enhances Suppliers Efficiency
When APQP is in place, suppliers become an integral part of the project team. They are working hand to hand with the APQP cross-functional team and they exactly know what will be required and expected from them well ahead of time.
They will not only know what’s required as per the specifications but will also be aware of how the quality will be gauged. APQP approach requires specific and tangible outcomes and provides standardised content whenever possible. This increases supplier’s efficiency and helps build a better relationship with them.
If you work within the aerospace industry, EQM Consult offers assistance in the implementation of the Advanced Product Quality Planning (APQP) and Production Part Approval Process (PPAP) according to AS 9145. Complete the contact form and we will be in touch with you to discuss how we can help.
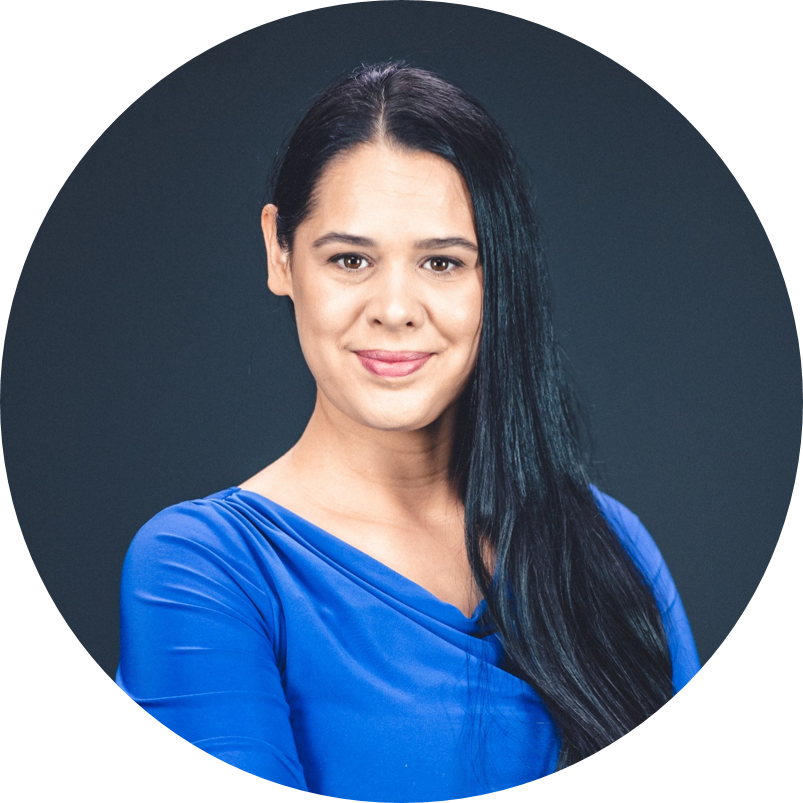
Ph.D. Beata Paliwoda
Founder and Owner of EQM. Environmental and quality consultant and auditor. Professional career built in Quality Assurance departments in various companies from the automotive, aerospace, railway industries, as well as a management systems consultant. Successfully completed many complex projects related to the implementation of management systems, process improvements and business transformation. Auditor of ISO 9001, ISO 14001, AS 9100, project manager of APM, lecturer at the Poznan University of Business and Economics, researcher on the effectiveness of EMS and QMS in organisations.